Lathe accidents are a significant concern in the manufacturing and machining industries, where workers frequently interact with these powerful machines. These accidents can result in severe injuries or even fatalities, highlighting the need for comprehensive safety protocols and awareness among operators. Understanding the causes and prevention of lathe accidents is crucial to ensuring a safe working environment and minimizing risks associated with machining operations.
The lathe machine is one of the oldest and most versatile tools used in machining, capable of shaping various materials such as metal, wood, and plastic. Despite their utility, lathes pose numerous hazards due to their rotating parts, sharp cutting tools, and the high-speed nature of their operations. This combination of factors makes it essential for operators to be well-trained and vigilant while working with lathes to prevent accidents.
In this comprehensive article, we will delve into the intricacies of lathe accidents, exploring their causes, the types of injuries they can inflict, and the safety measures that can be implemented to reduce their occurrence. We will also provide insights into how to respond effectively in the event of an accident and discuss the role of safety regulations and training in promoting a secure workplace. By the end of this article, readers will have a thorough understanding of lathe accidents and the necessary steps to mitigate their risks.
Table of Contents
- Understanding Lathes
- Common Causes of Lathe Accidents
- Types of Injuries from Lathe Accidents
- Safety Measures and Preventions
- Role of Training and Education
- Importance of Maintenance
- Case Studies of Lathe Accidents
- Emergency Response and First Aid
- Regulatory Standards and Guidelines
- Innovations in Lathe Safety
- Role of Technology in Accident Prevention
- Psychological Impact of Lathe Accidents
- Industry Best Practices
- Frequently Asked Questions
- Conclusion
Understanding Lathes
Lathes are essential tools in machining, designed to rotate a workpiece on its axis to perform various operations such as cutting, sanding, knurling, drilling, or deformation. The primary components of a lathe include the headstock, tailstock, bed, carriage, and tool post. These components work together to hold and manipulate the workpiece, allowing for precision machining.
There are several types of lathes, each suited for specific applications. These include engine lathes, turret lathes, and CNC lathes. Engine lathes are the most common and are highly versatile, while turret lathes are used for repetitive production tasks. CNC lathes, on the other hand, are computer-controlled, offering high precision and efficiency.
Despite their benefits, lathes are inherently dangerous due to their moving parts and sharp tools. Operators must understand the machine's operation thoroughly and adhere to safety protocols to prevent accidents. Proper maintenance and regular inspections are also crucial to ensure the lathe functions safely and efficiently.
Common Causes of Lathe Accidents
Lathe accidents can occur due to various factors, often resulting from operator error, equipment malfunction, or inadequate safety measures. One of the primary causes is the improper setup of the workpiece, leading to instability and potential ejection during operation. Additionally, using incorrect or dull tools can increase the risk of accidents by causing the tool to slip or break under pressure.
Another common cause is the lack of attention or focus from the operator, often due to fatigue or distraction. Inadequate training and experience can also contribute to accidents, as operators may not fully understand the machine's capabilities and limitations. Furthermore, failure to follow safety protocols, such as wearing appropriate personal protective equipment (PPE) or securing loose clothing and hair, can lead to severe injuries.
Equipment malfunction, such as faulty wiring or worn-out components, can also lead to accidents. Regular maintenance and inspections are essential to identify and address potential issues before they result in accidents. Ensuring that safety features, such as emergency stop buttons and guards, are functional and accessible is critical in minimizing risks.
Types of Injuries from Lathe Accidents
Lathe accidents can result in a wide range of injuries, from minor cuts and bruises to severe, life-threatening conditions. Some of the most common injuries include lacerations, fractures, and amputations, often caused by contact with rotating parts or sharp tools. These injuries can occur when operators reach over or near the machine without proper precautions or when they attempt to remove debris or adjust the workpiece while the lathe is in motion.
In addition to physical injuries, lathe accidents can also cause significant psychological trauma for the operator and witnesses. The sudden and often violent nature of these accidents can lead to stress, anxiety, and post-traumatic stress disorder (PTSD), affecting an individual's ability to work and their overall well-being.
To mitigate the risk of injuries, it is crucial for operators to follow safety guidelines, use appropriate PPE, and maintain a safe distance from moving parts. Employers should also provide regular training and mental health support to help workers cope with the aftermath of accidents.
Safety Measures and Preventions
Preventing lathe accidents requires a multifaceted approach, combining equipment safety, operator training, and workplace practices. One of the most effective safety measures is to ensure that all operators receive comprehensive training on lathe operation and safety protocols. This training should cover machine setup, tool selection, and the correct use of safety features such as guards and emergency stops.
Personal protective equipment (PPE) is another critical component of lathe safety. Operators should wear appropriate gear, including safety glasses, gloves, and protective clothing, to reduce the risk of injuries. It is also essential to secure loose clothing, jewelry, and hair to prevent entanglement with the machine.
Workplace practices, such as regular maintenance and inspections, play a vital role in preventing accidents. Ensuring that the lathe is in good working condition and that safety features are functional can significantly reduce the risk of equipment-related incidents. Additionally, promoting a culture of safety, where workers are encouraged to report hazards and near-misses, can help identify and address potential risks before they lead to accidents.
Role of Training and Education
Training and education are fundamental to preventing lathe accidents and ensuring a safe working environment. Comprehensive training programs should cover all aspects of lathe operation, including machine setup, tool selection, and safety protocols. These programs should be tailored to the specific needs of the workplace and regularly updated to incorporate new safety standards and technologies.
Education should also focus on developing a safety-first mindset among operators, encouraging them to prioritize safety over productivity. This can be achieved through regular safety meetings, workshops, and drills that reinforce the importance of following safety guidelines and using PPE.
Employers should also invest in ongoing training and certification programs to ensure that operators are up-to-date with the latest safety practices and technologies. By providing workers with the knowledge and skills they need to operate lathes safely, employers can significantly reduce the risk of accidents and create a safer workplace.
Importance of Maintenance
Regular maintenance is crucial for preventing lathe accidents and ensuring the machine operates safely and efficiently. Maintenance activities should include routine inspections, cleaning, and lubrication of components to prevent wear and tear. Any worn or damaged parts should be replaced promptly to avoid equipment malfunctions that could lead to accidents.
In addition to routine maintenance, operators should conduct pre-operation checks to ensure that the lathe is in good working condition. These checks should include verifying the functionality of safety features, such as guards and emergency stop buttons, and ensuring that tools and workpieces are securely mounted.
Employers should establish a maintenance schedule and assign qualified personnel to carry out these tasks. By prioritizing maintenance, companies can extend the lifespan of their equipment, reduce the risk of accidents, and minimize downtime due to repairs.
Case Studies of Lathe Accidents
Examining case studies of lathe accidents can provide valuable insights into the causes and consequences of these incidents, as well as highlight the importance of safety measures. One notable case involved a young operator who suffered severe injuries after his loose clothing became entangled in a rotating lathe. This accident underscored the need for proper PPE and the importance of securing clothing and accessories.
Another case involved an experienced machinist who lost several fingers while attempting to adjust a workpiece without stopping the machine. This incident highlighted the risks associated with complacency and the importance of adhering to safety protocols, regardless of experience level.
These case studies, among others, serve as cautionary tales and emphasize the need for continuous safety training, vigilance, and adherence to safety protocols. By learning from past accidents, companies can implement more effective safety measures and prevent similar incidents from occurring.
Emergency Response and First Aid
In the event of a lathe accident, a prompt and effective emergency response is crucial to minimizing injuries and providing the necessary care to the affected individual. Employers should establish clear emergency procedures and ensure that all workers are familiar with them. These procedures should include steps for shutting down the machine, calling for medical assistance, and providing first aid.
First aid training is essential for all workers, equipping them with the skills to respond quickly and effectively to injuries. This training should cover basic first aid techniques, such as controlling bleeding, treating lacerations, and addressing fractures. Having a well-stocked first aid kit readily available can also help ensure that workers have the necessary supplies to provide immediate care.
In addition to providing physical aid, it is important to offer emotional support to the injured worker and witnesses. The shock and trauma of witnessing or experiencing an accident can have lasting psychological effects, and providing access to mental health resources can aid in recovery.
Regulatory Standards and Guidelines
Regulatory standards and guidelines play a critical role in ensuring workplace safety and preventing lathe accidents. Organizations such as the Occupational Safety and Health Administration (OSHA) and the International Organization for Standardization (ISO) establish safety regulations that employers must follow to protect workers from hazards associated with lathe operations.
These regulations cover various aspects of lathe safety, including machine guarding, PPE requirements, and training standards. Employers must ensure compliance with these regulations to avoid legal repercussions and create a safe working environment for their employees.
In addition to adhering to regulatory standards, employers should stay informed about industry best practices and emerging safety technologies. By continuously improving safety measures and procedures, companies can reduce the risk of accidents and enhance overall workplace safety.
Innovations in Lathe Safety
Advancements in technology have led to significant innovations in lathe safety, providing new tools and solutions to prevent accidents and protect workers. One such innovation is the development of advanced machine guarding systems that provide enhanced protection against contact with rotating parts. These systems often include safety interlocks and sensors that automatically shut down the machine if a breach is detected.
Another innovation is the integration of automation and robotics in lathe operations, reducing the need for human intervention and minimizing the risk of accidents. Automated systems can perform tasks such as tool changes and workpiece adjustments, allowing operators to focus on monitoring and controlling the process from a safe distance.
Wearable technology, such as smart PPE, is also gaining traction in the industry, providing real-time monitoring of workers' health and safety. These devices can track vital signs, detect fatigue, and alert operators to potential hazards, helping to prevent accidents before they occur.
Role of Technology in Accident Prevention
Technology plays a crucial role in preventing lathe accidents by enhancing safety measures and providing new tools for monitoring and control. Computer numerical control (CNC) technology, for example, allows for precise and automated machining, reducing the risk of operator error and improving overall safety.
Advanced sensors and monitoring systems can detect anomalies in machine operation, such as vibrations or overheating, and alert operators to potential issues before they lead to accidents. These systems can also be integrated with predictive maintenance software to identify and address equipment malfunctions proactively.
Virtual reality (VR) and augmented reality (AR) technologies are also being used for training purposes, providing operators with realistic simulations of lathe operations and safety scenarios. These immersive training tools allow workers to practice and develop their skills in a controlled environment, reducing the likelihood of accidents on the shop floor.
Psychological Impact of Lathe Accidents
The psychological impact of lathe accidents can be profound, affecting not only the injured worker but also their colleagues and the workplace as a whole. The sudden and often traumatic nature of these incidents can lead to stress, anxiety, and PTSD, impacting an individual's ability to work and their overall quality of life.
Employers should recognize the importance of addressing the psychological effects of accidents and provide access to mental health resources for affected workers. This can include counseling services, support groups, and stress management programs to help individuals cope with the aftermath of an accident.
Creating a supportive and open workplace culture where workers feel comfortable discussing their experiences and seeking help is essential for promoting recovery and well-being. By prioritizing mental health and providing the necessary support, employers can help workers overcome the psychological challenges associated with lathe accidents.
Industry Best Practices
Implementing industry best practices is essential for preventing lathe accidents and ensuring a safe working environment. These practices include conducting regular safety audits and risk assessments to identify potential hazards and address them proactively. Employers should also establish clear safety policies and procedures, providing workers with the necessary guidance and resources to operate lathes safely.
Encouraging a culture of safety, where workers are actively involved in identifying and reporting hazards, is also crucial for preventing accidents. Employers can promote this culture by recognizing and rewarding safe behavior, providing regular safety training, and fostering open communication between workers and management.
By adopting industry best practices and continuously improving safety measures, companies can reduce the risk of lathe accidents and create a safer, more productive workplace for their employees.
Frequently Asked Questions
- What are the most common causes of lathe accidents?
Common causes include operator error, equipment malfunction, improper setup, and inadequate safety measures.
- How can lathe accidents be prevented?
Prevention involves comprehensive training, use of PPE, regular maintenance, adherence to safety protocols, and promoting a safety-first culture.
- What types of injuries are associated with lathe accidents?
Injuries can range from minor cuts and bruises to severe lacerations, fractures, and amputations, as well as psychological trauma.
- What role does technology play in preventing lathe accidents?
Technology enhances safety through advanced machine guarding, automation, sensors, and training tools like VR and AR simulations.
- What are the regulatory standards for lathe safety?
Organizations like OSHA and ISO establish safety regulations covering machine guarding, PPE requirements, and training standards.
- How should one respond in the event of a lathe accident?
Follow established emergency procedures, provide first aid, call for medical assistance, and offer emotional support to affected individuals.
Conclusion
Lathe accidents pose significant risks in the machining industry, with the potential for severe injuries and psychological trauma. However, by understanding the causes and implementing effective safety measures, these accidents can be prevented. Comprehensive training, adherence to safety protocols, regular maintenance, and the integration of technology all play crucial roles in minimizing risks and ensuring a safe working environment. By fostering a culture of safety and prioritizing both physical and mental well-being, employers can protect their workers and promote a productive and secure workplace.
For further information on lathe safety standards and best practices, visit the Occupational Safety and Health Administration's website: OSHA.

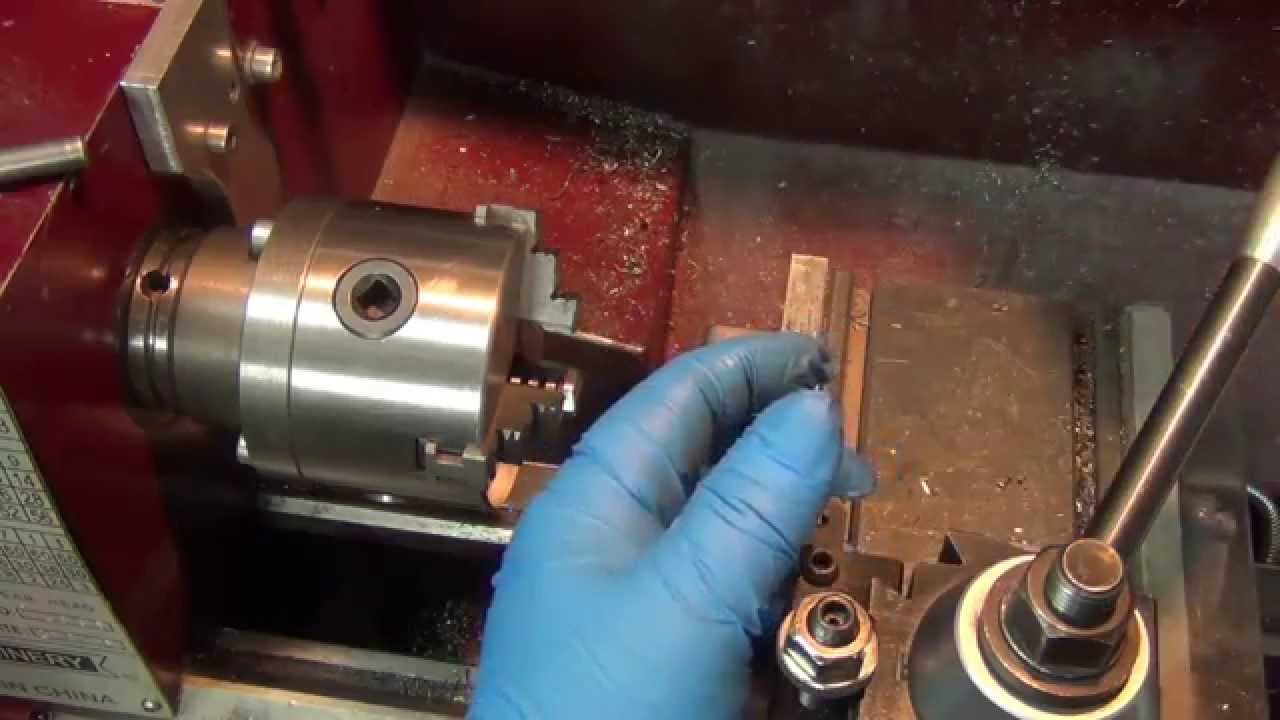
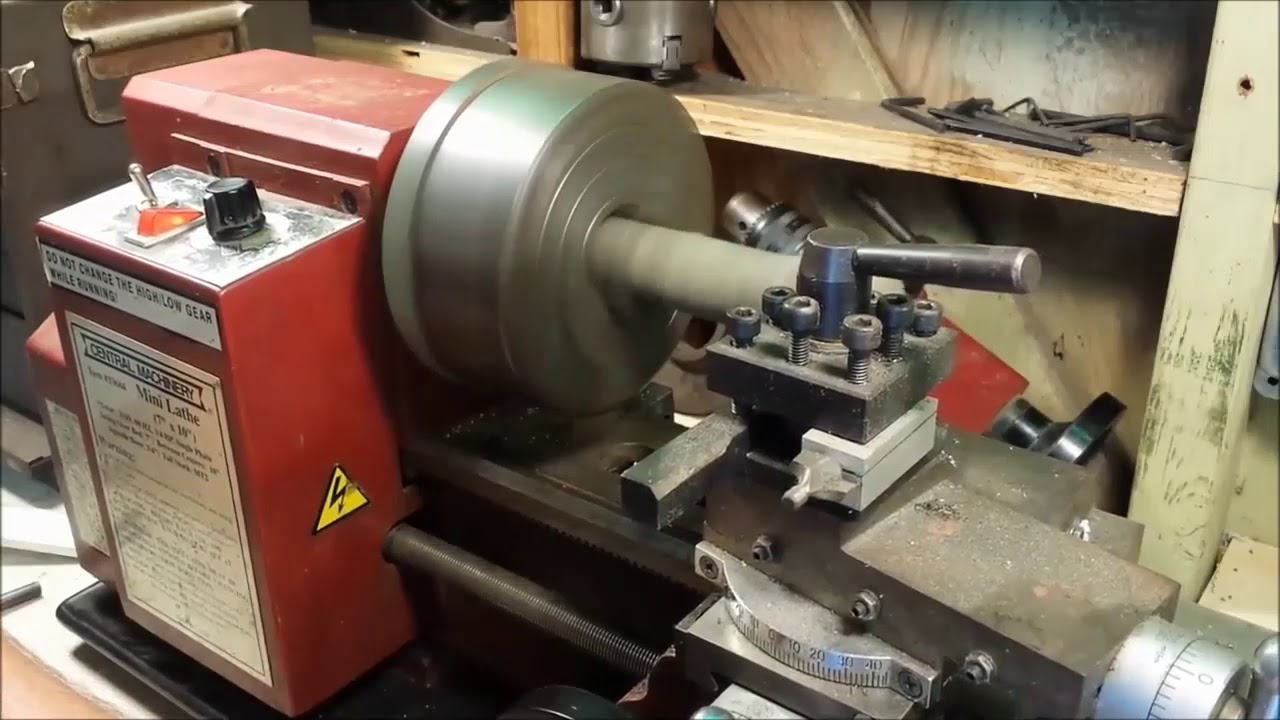