In the industrial landscape, the presence of machinery plays a pivotal role in enhancing productivity and efficiency. However, it also comes with its share of risks. One such risk is associated with the use of lathes, a common machine tool in manufacturing industries. Lathe accident videos have surfaced online, highlighting the potential dangers of this equipment. These videos often serve as cautionary tales, demonstrating the severe consequences that can occur if safety protocols are not strictly followed. Understanding these incidents is crucial for preventing future accidents and ensuring workplace safety.
Lathe machines, renowned for their versatility and functionality, are integral to various manufacturing processes. They are used to shape materials such as metal and wood by rotating the workpiece against a cutting tool. Despite their utility, lathes can be extremely dangerous if mishandled or if safety precautions are ignored. The lathe accident videos circulating on the internet have brought significant attention to the importance of adhering to safety measures while operating these machines. By analyzing these videos, workers and employers alike can learn valuable lessons to avert similar mishaps.
The impact of a lathe accident extends beyond immediate physical harm; it can also lead to psychological trauma, financial losses, and operational disruptions. Thus, it is imperative to foster a culture of safety in workplaces where lathes and other machinery are utilized. Employers must invest in comprehensive training programs, regular equipment maintenance, and a robust safety protocol to protect their workforce. This article delves into the intricacies of lathe accidents, examining their causes, consequences, and preventive measures, to equip readers with the knowledge needed to safely navigate the use of these powerful machines.
Table of Contents
- Understanding Lathe Machines
- Common Causes of Lathe Accidents
- Impact of Lathe Accidents
- Safety Guidelines for Lathe Operation
- Case Studies of Lathe Accidents
- Importance of Training and Education
- Role of Employers in Preventing Accidents
- Technological Advancements in Lathe Safety
- Psychological and Financial Implications
- Legislation and Standards
- Emergency Response Procedures
- Future Prospects
- Frequently Asked Questions
- Conclusion
Understanding Lathe Machines
Lathe machines are essential tools in the manufacturing industry, known for their ability to shape and cut materials with precision. These machines work by rotating the workpiece on its axis while a stationary cutting tool removes material to create the desired shape. The components of a lathe machine include the bed, headstock, tailstock, carriage, and spindle, each playing a crucial role in its operation.
There are various types of lathes, including wood lathes, metal lathes, and CNC (Computer Numerical Control) lathes. Each type serves a specific purpose and is designed to handle different materials and levels of complexity. For instance, wood lathes are used for woodworking projects, whereas metal lathes are employed in metal fabrication industries. CNC lathes, on the other hand, offer advanced capabilities with computer-controlled precision, making them ideal for high-volume production.
The versatility of lathe machines makes them indispensable in sectors such as automotive, aerospace, and construction. However, this versatility also necessitates a thorough understanding of their operation and potential hazards. Operators must be well-versed in machine setup, speed selection, tool positioning, and other technical aspects to ensure efficient and safe usage.
Despite their functionality, lathe machines pose significant risks if not operated correctly. The high-speed rotation of workpieces can lead to severe injuries if safety measures are not observed. Thus, it is vital for operators to receive adequate training and adhere to safety protocols to prevent accidents and ensure a secure working environment.
Common Causes of Lathe Accidents
Lathe accidents can occur due to a variety of reasons, often stemming from human error, equipment malfunction, or inadequate safety measures. One of the primary causes is lack of proper training, which leads to incorrect machine handling and operation. When operators are not fully trained, they are more likely to make mistakes that can result in accidents.
Another common cause is the failure to adhere to safety protocols. This includes not wearing appropriate personal protective equipment (PPE) such as gloves, goggles, and helmets, as well as neglecting to follow established safety procedures. Additionally, distractions or complacency in the workplace can lead to lapses in concentration, increasing the risk of accidents.
Equipment malfunction or poor maintenance is also a significant factor in lathe accidents. Worn-out parts, loose components, or improper machine setup can lead to catastrophic failures during operation. Regular maintenance checks and prompt repairs are crucial to ensuring the reliability and safety of lathe machines.
Furthermore, the improper use of tools and accessories can contribute to accidents. Using the wrong tool for a specific job or failing to secure the workpiece adequately can cause the lathe to operate unpredictably, posing a danger to the operator and surrounding personnel.
Identifying and addressing these common causes is essential for minimizing the risk of lathe accidents. By implementing comprehensive training programs, enforcing strict safety protocols, and maintaining equipment regularly, employers can create a safer working environment and protect their workforce from potential hazards.
Impact of Lathe Accidents
Lathe accidents can have far-reaching consequences, affecting not only the individuals involved but also the organization as a whole. The immediate impact is often physical injury, ranging from minor cuts and bruises to severe trauma such as amputations or even fatalities. These injuries can result in significant medical expenses, prolonged recovery periods, and, in some cases, permanent disability.
Beyond the physical harm, lathe accidents can also lead to psychological trauma for the affected individuals. Experiencing a traumatic incident at work can result in anxiety, depression, or post-traumatic stress disorder (PTSD), impacting the individual's overall well-being and ability to perform in their role.
From an organizational perspective, lathe accidents can lead to financial losses due to increased insurance premiums, compensation claims, and potential legal liabilities. Moreover, accidents can disrupt production schedules, resulting in lost productivity and potential revenue losses. The damage to equipment and the cost of repairs or replacements further contribute to the financial burden.
Lathe accidents can also tarnish an organization's reputation, affecting its relationships with clients, partners, and employees. A company known for frequent workplace accidents may struggle to attract and retain talent, as well as secure business opportunities.
To mitigate these impacts, it is crucial for organizations to prioritize safety and invest in preventive measures. By fostering a culture of safety, providing comprehensive training, and maintaining equipment, employers can reduce the likelihood of accidents and their associated consequences.
Safety Guidelines for Lathe Operation
Ensuring safety while operating lathe machines is paramount to preventing accidents and protecting workers. Adhering to established safety guidelines can significantly reduce the risk of incidents and create a safer working environment.
One of the fundamental safety measures is providing comprehensive training for all operators. Training should cover the proper use of the lathe, machine setup, tool selection, and safety protocols. Operators should be familiar with the machine's components and functions, enabling them to identify potential hazards and respond appropriately.
Wearing appropriate personal protective equipment (PPE) is essential to safeguard against potential injuries. Operators should wear gloves, goggles, helmets, and other protective gear to shield themselves from flying debris, sharp edges, and other risks associated with lathe operation.
Maintaining a clean and organized workspace is another critical safety measure. Clutter and debris can pose tripping hazards and obstruct access to emergency exits. Keeping the work area tidy and free from unnecessary items can enhance safety and efficiency.
Regular equipment maintenance and inspections are crucial for ensuring the reliability and safety of lathe machines. Employers should implement routine checks to identify and address any wear and tear, loose components, or other issues that could compromise safety. Prompt repairs and replacements should be carried out to maintain the machine's integrity.
Enforcing strict safety protocols and procedures is vital for minimizing risks. Employers should establish clear guidelines for lathe operation, including speed limits, tool selection, and emergency response procedures. Operators should be encouraged to report any safety concerns or incidents promptly.
By adhering to these safety guidelines, organizations can create a safer working environment and protect their workforce from the potential dangers of lathe operation.
Case Studies of Lathe Accidents
Examining real-life case studies of lathe accidents provides valuable insights into the potential risks and consequences of mishandling these machines. By analyzing past incidents, we can identify common factors and implement preventive measures to avoid similar accidents in the future.
One notable case involved an operator who suffered severe injuries after being caught in a lathe's rotating parts. The accident occurred due to the operator's failure to follow safety protocols, including wearing appropriate PPE and securing loose clothing. This case highlights the importance of adhering to safety guidelines and maintaining awareness of potential hazards.
Another incident involved a lathe machine malfunction, resulting in the workpiece being ejected at high speed. The operator sustained significant injuries, and the machine was severely damaged. An investigation revealed that inadequate maintenance and inspections contributed to the equipment failure. This case underscores the necessity of regular maintenance checks and timely repairs to ensure machine safety and reliability.
In a separate case, an inexperienced operator attempted to use a lathe without proper training, leading to an accident that resulted in multiple injuries. This incident emphasizes the critical role of training and education in preventing accidents and protecting workers.
By learning from these case studies, organizations can identify potential risks and implement measures to prevent similar accidents. Ensuring proper training, adhering to safety protocols, and maintaining equipment are essential steps in creating a safer working environment.
Importance of Training and Education
Training and education play a pivotal role in preventing lathe accidents and ensuring the safety of operators. Comprehensive training programs equip workers with the knowledge and skills needed to operate lathe machines safely and efficiently.
Training should cover various aspects of lathe operation, including machine setup, tool selection, speed adjustment, and safety protocols. Operators should be familiar with the machine's components and functions, enabling them to identify potential hazards and respond appropriately.
In addition to technical training, operators should receive instruction on the importance of personal protective equipment (PPE) and safe work practices. Understanding the significance of PPE and adhering to established safety protocols can significantly reduce the risk of accidents and injuries.
Ongoing education and refresher courses are essential for keeping operators updated on the latest safety standards and best practices. Regular training sessions can reinforce the importance of safety and ensure that operators remain vigilant and informed.
Employers play a crucial role in facilitating training and education for their workforce. By investing in comprehensive training programs and fostering a culture of safety, organizations can protect their employees and create a safer working environment.
Role of Employers in Preventing Accidents
Employers bear a significant responsibility in preventing lathe accidents and ensuring the safety of their workforce. By implementing robust safety measures and fostering a culture of safety, employers can protect their employees and reduce the risk of incidents.
One of the primary responsibilities of employers is to provide comprehensive training and education for all operators. Training programs should cover the proper use of lathe machines, safety protocols, and the importance of personal protective equipment (PPE). Ensuring that operators are well-trained and informed is crucial for preventing accidents and injuries.
Employers should also enforce strict safety protocols and procedures, including regular equipment maintenance and inspections. Routine checks can identify potential issues and ensure that lathe machines remain safe and reliable. Prompt repairs and replacements should be carried out to address any wear and tear or malfunctions.
Creating a safe and organized work environment is another critical aspect of accident prevention. Employers should maintain a clean and clutter-free workspace, minimizing hazards and ensuring easy access to emergency exits.
Encouraging open communication and reporting of safety concerns is essential for identifying potential risks and addressing them promptly. Employers should foster a culture of safety where workers feel comfortable reporting hazards or incidents without fear of retribution.
By fulfilling their responsibilities and prioritizing safety, employers can create a safer working environment and protect their workforce from the potential dangers of lathe operation.
Technological Advancements in Lathe Safety
Technological advancements have significantly enhanced lathe safety, providing operators with innovative tools and features to minimize risks and prevent accidents. These advancements have transformed traditional lathe machines, making them safer and more efficient for modern manufacturing processes.
One notable advancement is the integration of computer numerical control (CNC) technology in lathe machines. CNC lathes offer precise control and automation, reducing the need for manual intervention and minimizing the risk of human error. With CNC technology, operators can program and monitor the machine's operations, ensuring accuracy and safety.
Safety interlocks and sensors are another technological enhancement that has improved lathe safety. These features automatically shut down the machine in the event of a malfunction or unsafe condition, preventing accidents and protecting operators. Safety sensors can detect anomalies such as excessive vibration or temperature, alerting operators to potential hazards.
Advanced guarding systems have also been developed to protect operators from flying debris and rotating parts. These systems provide physical barriers that prevent access to hazardous areas while allowing operators to monitor the machining process safely.
Moreover, ergonomic designs and user-friendly interfaces have made lathe machines more accessible and safer for operators. These features reduce operator fatigue and improve overall efficiency, further enhancing safety in the workplace.
As technology continues to evolve, we can expect further advancements in lathe safety, providing operators with even more tools and features to ensure a secure working environment.
Psychological and Financial Implications
Lathe accidents can have profound psychological and financial implications, affecting both individuals and organizations. The psychological impact of an accident can be significant, leading to anxiety, depression, or post-traumatic stress disorder (PTSD) for the affected individuals. Experiencing a traumatic incident at work can affect an individual's overall well-being and ability to perform in their role.
From a financial perspective, lathe accidents can result in substantial costs for organizations. Medical expenses, compensation claims, and increased insurance premiums can contribute to financial losses. Additionally, accidents can disrupt production schedules, resulting in lost productivity and potential revenue losses.
The cost of equipment repairs or replacements further adds to the financial burden. Damaged machinery may require extensive repairs or even replacement, leading to additional expenses for the organization.
Furthermore, lathe accidents can damage an organization's reputation, affecting its relationships with clients, partners, and employees. A company known for frequent workplace accidents may struggle to attract and retain talent, as well as secure business opportunities.
To mitigate these psychological and financial implications, organizations must prioritize safety and invest in preventive measures. By fostering a culture of safety, providing comprehensive training, and maintaining equipment, employers can reduce the likelihood of accidents and their associated consequences.
Legislation and Standards
Legislation and standards play a crucial role in ensuring lathe safety and protecting workers from potential hazards. Various national and international regulations and standards have been established to guide the safe operation of lathe machines and other industrial equipment.
In many countries, occupational health and safety laws mandate the implementation of safety measures and protocols for machinery operation. These laws require employers to provide adequate training, personal protective equipment (PPE), and a safe working environment for their employees.
Standards organizations such as the International Organization for Standardization (ISO) and the American National Standards Institute (ANSI) have developed specific standards for lathe safety. These standards outline requirements for machine design, guarding, and operation, providing a framework for manufacturers and operators to ensure compliance and safety.
Compliance with these regulations and standards is essential for minimizing the risk of accidents and protecting workers. Employers must stay informed about the latest legislation and standards and ensure that their operations align with these requirements.
Regular audits and inspections can help organizations identify areas of non-compliance and implement corrective measures. By adhering to legislation and standards, employers can create a safer working environment and reduce the risk of lathe accidents.
Emergency Response Procedures
Emergency response procedures are critical for ensuring a swift and effective response to lathe accidents and other workplace incidents. Having a well-defined plan in place can minimize the impact of an accident and protect the safety of workers.
One of the first steps in developing emergency response procedures is conducting a risk assessment to identify potential hazards and assess the likelihood of accidents. This assessment can help organizations prioritize their response efforts and allocate resources effectively.
Emergency response procedures should include clear guidelines for reporting accidents, evacuating the area, and providing first aid. Employees should be trained on these procedures and know how to respond in the event of an emergency.
Employers should also establish communication protocols for notifying emergency services and relevant personnel. Having a designated point of contact for emergencies can ensure a coordinated response and facilitate communication with external agencies.
Regular drills and simulations can help employees practice their response and ensure that they are familiar with the procedures. These exercises can also help identify any gaps or areas for improvement in the emergency response plan.
By developing and implementing comprehensive emergency response procedures, organizations can enhance their preparedness and protect the safety of their workforce in the event of an accident.
Future Prospects
The future of lathe safety is likely to be shaped by continued technological advancements and increased emphasis on safety standards and training. As technology evolves, we can expect further innovations that enhance the safety and efficiency of lathe machines.
Automation and robotics are expected to play an increasingly significant role in lathe operation, further reducing the need for manual intervention and minimizing the risk of human error. These technologies can improve precision and consistency, enhancing safety and productivity in the manufacturing process.
Advancements in sensors and monitoring systems are also likely to enhance lathe safety. These technologies can provide real-time data on machine performance and detect potential hazards, enabling operators to respond proactively and prevent accidents.
Increased emphasis on safety standards and training is expected to drive further improvements in lathe safety. Organizations are likely to invest more in comprehensive training programs and adhere to stricter safety protocols to protect their workforce.
Overall, the future prospects for lathe safety are promising, with continued advancements and focus on safety expected to create a safer working environment for operators.
Frequently Asked Questions
- What are the common causes of lathe accidents?
Common causes include lack of proper training, failure to follow safety protocols, equipment malfunction, and improper use of tools.
- How can lathe accidents be prevented?
Lathe accidents can be prevented by providing comprehensive training, adhering to safety protocols, maintaining equipment, and ensuring operators wear appropriate PPE.
- What is the role of employers in preventing lathe accidents?
Employers are responsible for providing training, enforcing safety protocols, maintaining equipment, and fostering a culture of safety.
- What are the psychological implications of lathe accidents?
Lathe accidents can lead to psychological trauma, including anxiety, depression, and PTSD, affecting the individual's well-being and ability to work.
- How do technological advancements enhance lathe safety?
Technological advancements, such as CNC technology, safety sensors, and advanced guarding systems, enhance precision, reduce human error, and protect operators from hazards.
- What are emergency response procedures for lathe accidents?
Emergency response procedures include reporting accidents, evacuating the area, providing first aid, and communicating with emergency services. Regular drills and training ensure preparedness.
Conclusion
In conclusion, lathe accident videos serve as stark reminders of the potential dangers associated with operating these powerful machines. Understanding the causes and consequences of lathe accidents is crucial for preventing future incidents and ensuring workplace safety. By adhering to safety guidelines, providing comprehensive training, and investing in technological advancements, employers can protect their workforce and create a safer working environment. As technology continues to evolve, the future prospects for lathe safety are promising, offering new opportunities to enhance safety and efficiency in the manufacturing industry.


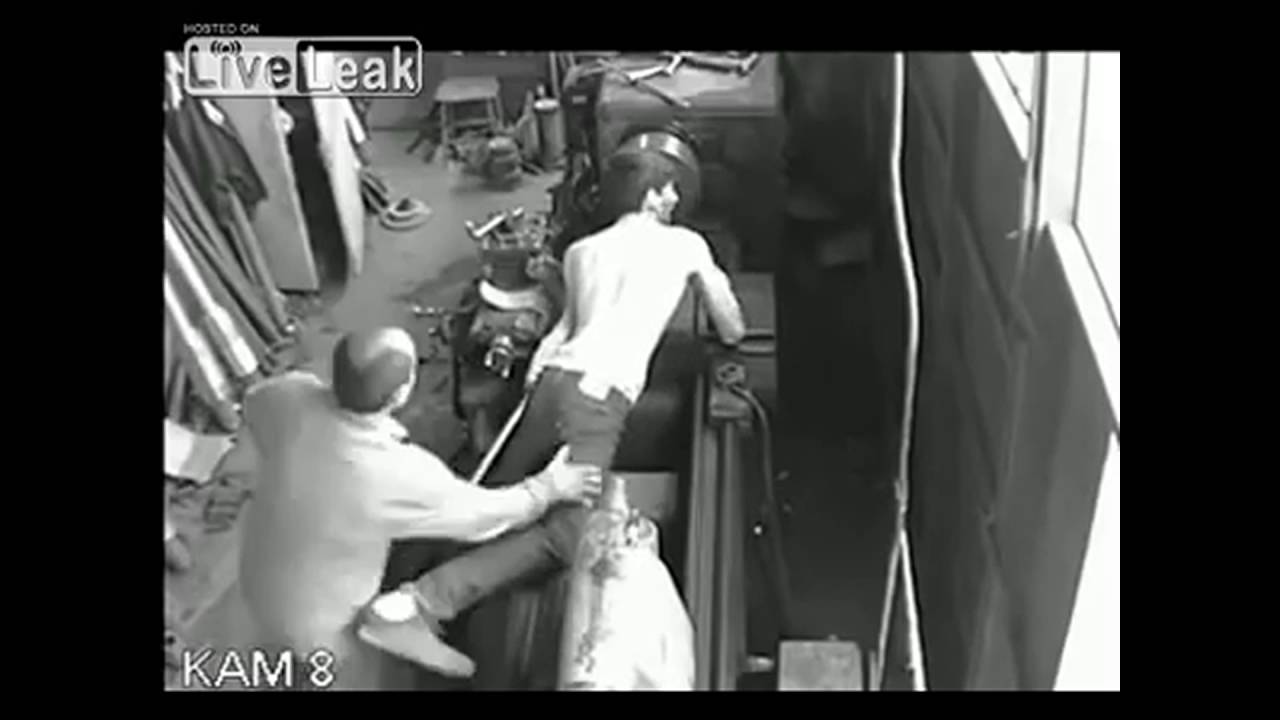